Automation Use Case: Enforcing Daily Safety Protocols on Construction Job Sites
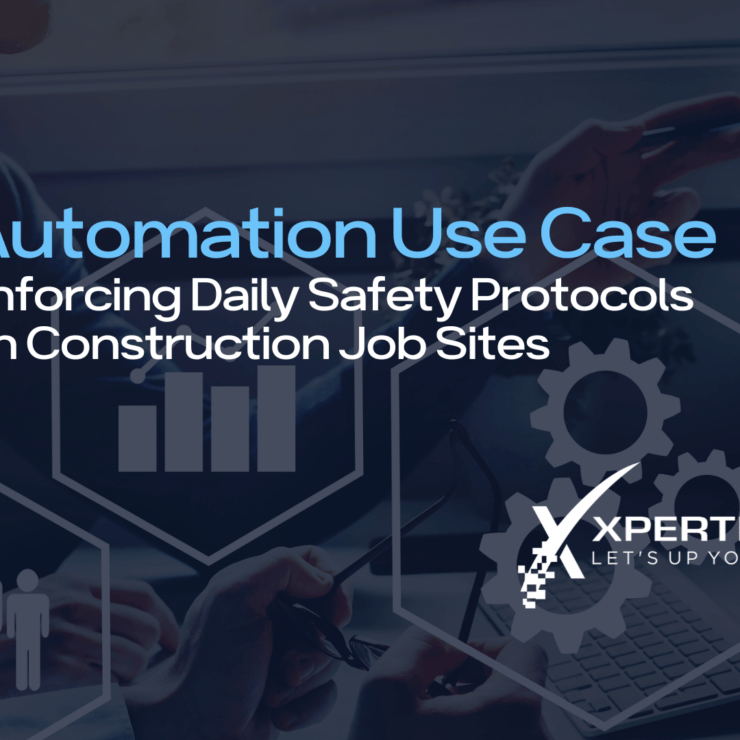
When safety procedures are handled informally, important steps can fall through the cracks. That’s what was happening at a construction company where field engineers were expected to complete a daily safety check-in at job sites. The process lacked consistency, and the supervisor overseeing it had no clear way to tell who was following through, or why others weren’t.
What started as a request for better visibility led to a mobile-friendly app, real-time reporting, and a much stronger system for enforcing safety protocols.
The Problem
The company had a safety process in place. Engineers on site were expected to confirm the presence and use of proper safety equipment through a daily check-in. But in practice, the process was informal and often overlooked. Key issues included:
- Safety check-ins were handled inconsistently. Some engineers added a note in their project reports to say safety protocols were followed, while others skipped the step entirely.
- The supervisor responsible for enforcing the process couldn’t tell who had submitted the daily safety check-in and who hadn’t.
- There was no structured way to follow up, hold people accountable, or identify patterns of noncompliance.
- Missed check-ins introduced risk and made it difficult to confirm that PPE was used or protocols were followed, leaving the company exposed in case of an audit or incident.
The Solution
XPERTECHS developed a mobile-friendly app with two core functions: daily check-in and supervisor oversight, backed by structured reporting tools.
- Mobile Check-In Form: Engineers complete a short form from their phones each day they’re on site. The form captures key information, including which safety equipment was present, who was on the job, and who was responsible for the project.
- Supervisor Dashboard: Inside the app, a simple dashboard shows who submitted the form each day and who didn’t. It’s designed for quick, daily oversight so supervisors can follow up in real time.
- Automated Notifications: Engineers receive both an email and a text message each day prompting them to complete the check-in. Links in the notifications take them straight to the form.
- Power BI Reporting: For broader visibility, the data feeds into Power BI. Leadership can use interactive dashboards to track compliance trends, identify repeat gaps, and generate visual reports to support audits or internal reviews.
- Audit-Ready Recordkeeping: Submissions are stored with full detail, including names, roles, dates, listed PPE, and project assignments. If an OSHA audit or internal investigation is needed, records can be retrieved instantly and matched to specific days.
Key Outcomes
Stronger Oversight and Accountability
For the first time, the supervisor had full visibility into who was completing the safety check-in and who wasn’t. Inconsistent compliance became easier to spot and address. The system supported more consistent follow-up and led to changes in management practices, including disciplinary action when required.
Simpler Process, Higher Compliance
By making the process easy to complete and harder to ignore, compliance improved. Engineers receive automated reminders and can fill out the form on their phones in just a few taps. There’s no need to remember to write something down or send a report later.
Searchable Records and Audit Readiness
The app creates a daily, time-stamped record for each safety check-in. All entries are stored in a structured, accessible format that makes it easy to locate specific reports. Whether for an OSHA audit, an internal review, or a specific incident date, the data is available and organized.
Data-Driven Visibility at Every Level
The system provides value beyond daily oversight. Supervisors use the in-app dashboard to manage daily compliance, while leadership teams rely on Power BI reporting to spot trends, identify recurring issues, and assess how consistently safety protocols are being followed across job sites. Having structured data readily available has made it easier to hold teams accountable and prepare for conversations with regulators or internal stakeholders.
Applying Automation to Other Industries
This type of automation is especially valuable in any industry where compliance depends on consistent follow-through in the field. Similar systems could be used to track:
Manufacturing: Shift handoffs, machine safety checks, or PPE logs.
Healthcare: Daily sanitation forms, incident reports, or staff credential tracking.
Field Service Teams: Time-on-site verification, job completion logs, or safety confirmations.
Energy and Utilities: Environmental checks, hazard reports, or technician activity logs.
Financial Services: Daily compliance checklists, audit documentation, or task attestation workflows
From Informal Process to Enforceable System
This construction company didn’t need to overhaul its safety strategy. It just needed a consistent, trackable way to enforce it. By automating the check-in process, they gained the visibility, accountability, and reporting tools that make compliance practical every single day.
Business Process Automation Expertise
XPERTECHS works with organizations to turn manual, informal workflows into reliable systems. If you’re ready to strengthen your safety process or enforce critical protocols with better tools, let’s talk.
Learn more about business process automation solutions from XPERTECHS.
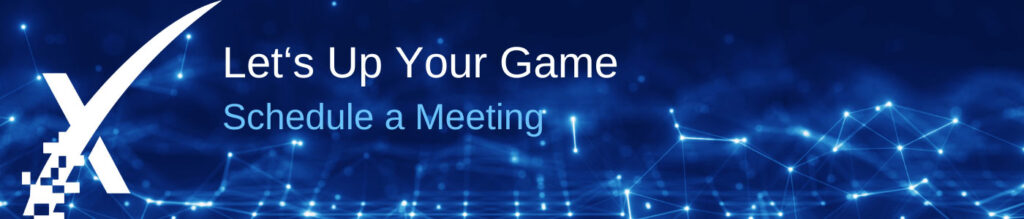